Environmental audit program - Industries in focus
In order to achieve an ecologically sustainable Inner West, Council routinely undertakes pro-active environmental audits of a variety of premises and industries.
Our environmental auditing program assists business and industry to understand what is required and adopt a more proactive role in protecting the environment and human health.
Council’s environmental auditing program assess premises against relevant environmental guidelines and the development approval to ensure impacts to our environment are appropriately and adequately mitigated.
Environmental audit objectives include:
- To provide environmental education
- To ensure adherence to development approvals
- To ensure adherence to statutory requirements
- To improve environmental management outcomes
In addition, Council regularly undertakes environmental regulatory and clean-up work based on observations, reports from the community or in association with emergencies.
Underground Petroleum Storage Systems (UPSS) & Vapour Recovery at Service Stations
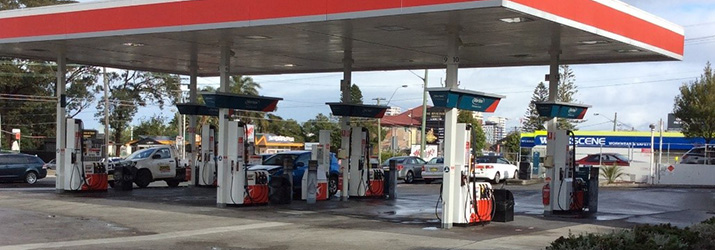
On 1 September 2019, Council resumed responsibility for regulation of Underground Petroleum Storage System (UPSS) sites from the Environmental Protection Authority (EPA).
We have now implemented an environmental education program specifically for the petroleum industry.
The program aims to educate petroleum industry operators and stakeholders about their legislative obligations as well as best practice design, installation, maintenance, and monitoring of Underground Petroleum Storage Systems (UPSS) and Vapour Recovery systems.
The person responsible for the UPSS has a duty to notify pollution incidents immediately and then provide a completed UPSS leak notification form to Council within 7 days.
Report a leak
To report a leak complete the form below and return to Council by:
Email: Council@innerwest.nsw.gov.au
Mail:
Inner West Council
PO Box 14,
Petersham NSW 2049
Leak notification form (UPSS) (PDF 179.3KB)
Leak notification form (UPSS) (DOCX 78.2KB)
Inspection check lists may include:
Vapour Recovery Systems Inspection
- Tank integrity test report
- Vapour recovery (VR1/VR2) commissioning report
- Evidence of VR1/VR2 control equipment installed (evidence if not required)
- Periodic testing report of prescribed storage tank and control equipment fitted to the tank (e.g. pressure vacuum valve and 10 mm orifice)
- Logbook (must contain above mention documents and receipts/invoices for any repairs of significant faults or general maintenance/repairs)
N.B: Fuel System Operation Plan (FSOP) can be regarded as logbook if that contains above mentioned documents along with FSOP requirements.
UPSS inspection
Fuel System Operation Plan (FSOP) previously known as Environmental Protection Plan. The folder must contain the followings;
- Responsible person's contact details
- Site security details
- Total annual fuel sales records (showing monthly throughput and throughout)
- Loss Monitoring Records (i.e. SIRA reports, Manual Dipping records)
- Leak Detection Records –(6-monthly Ground Water Monitoring Well records)
- UPSS Maintenance schedule and records
- Record of any significant modifications to the system
- Current ‘as-built’ drawings for the system
- Site plan (to scale including: all tanks, fill points, pipelines, all buildings and infrastructure, all groundwater monitoring wells, any unsealed ground surfaces, fences and gates, drainage and services, and adjacent land use)
- Staff training manual and attendance records.
Forecourt management issues
- Trade waste agreements
- Stormwater/Groundwater management
- Groundwater Monitoring
- Forecourt design
- Oil Water Separator use & maintenance
- Backflow protection
- Spill response – Spill Kit, emergency management plan
- Materials management – Storage of chemicals, , Material Safety Data Sheet (MSDS)
- Waste management – appropriate disposal of hazardous / contaminated chemicals or materials, waste tracking receipts, recycling facilities;
- Air and noise emissions – Use of compressors
- Resource efficiency/Sustainability – energy use
Educational resources
Automotive Repair Industry
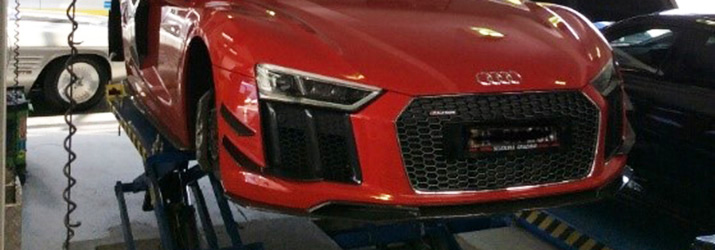
Inner West Council is home to approximately 150 automotive mechanical repair premises and approximately 50 smash repair premises which may if appropriate measures are not implemented pose a risk to the environment. Council’s Environmental Audit Program aims to help businesses operate in more environmentally friendly way.
The Department of Environment and Climate Change NSW (DECC) and Environmental Protection Authority NSW (EPA) provided guidelines for Automotive Mechanical and Smash repairs industry. For more information, please see the link in the Educational material section.
Inspection check lists may include:
- Air quality
- Water quality
- Bunding
- Noise management
- Hazardous substance and chemical storage
- Dust control measures
- Spill management/emergency plan
- Stormwater management
- Oil-water separator or alternate water treatment system
- Solid liquid waste management
- Spray booth and filters
Educational resources
Car Wash Industry
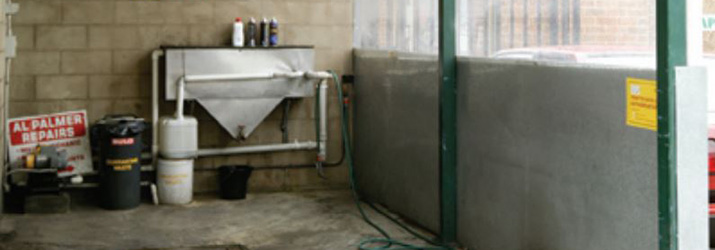
Inner West Council is home to approximately 30 car wash business. The primary concern of a car wash business is wash water drainage. Car wash water contains chemical, oil, grease, dirt and grime that can degrade water quality. Our education program aims to ensure that the car wash water is not discharged to storm water system. Appropriate bunding must be installed to prevent car wash water from escaping into storm water system. Council encourages to install wastewater treatment system/ water separator in the premises.
Inspection check lists may include:
- Air quality
- Water quality
- Bunding
- Noise management
- Hazardous substance and chemical storage
- Dust control measures
- Spill management/emergency plan
- Stormwater management
- Oil-water separator or alternate water treatment system
- Solid Liquid waste management
Educational resources
Marinas, Boatsheds & Slipways
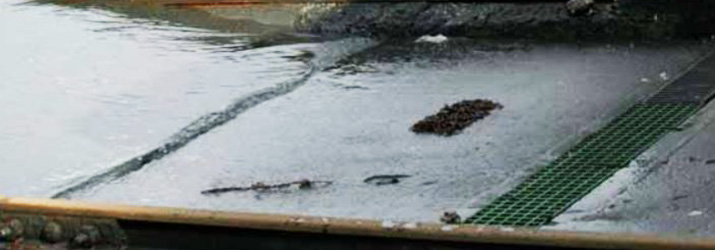
Inner West is also a home to a few marinas where Council is Appropriate Regulatory Authority (ARA). Council conducts audits to educate marina operators about the environmental risks and responsibilities associated with the boating industry.
Key environmental issues for marinas, boatsheds and slipways are air, water, land and noise pollution. Council encourages operators to take action to improve the environmental management of their operations.
Inspection check lists may include:
- Air quality
- Water quality
- Bunding
- Noise management
- Hazardous substance and chemical storage
- Dust control measures
- Spill management/emergency plan
- Stormwater management
- Oil-water separator or alternate water treatment system
- Solid liquid waste management
- Spray booth and filters
Educational resources